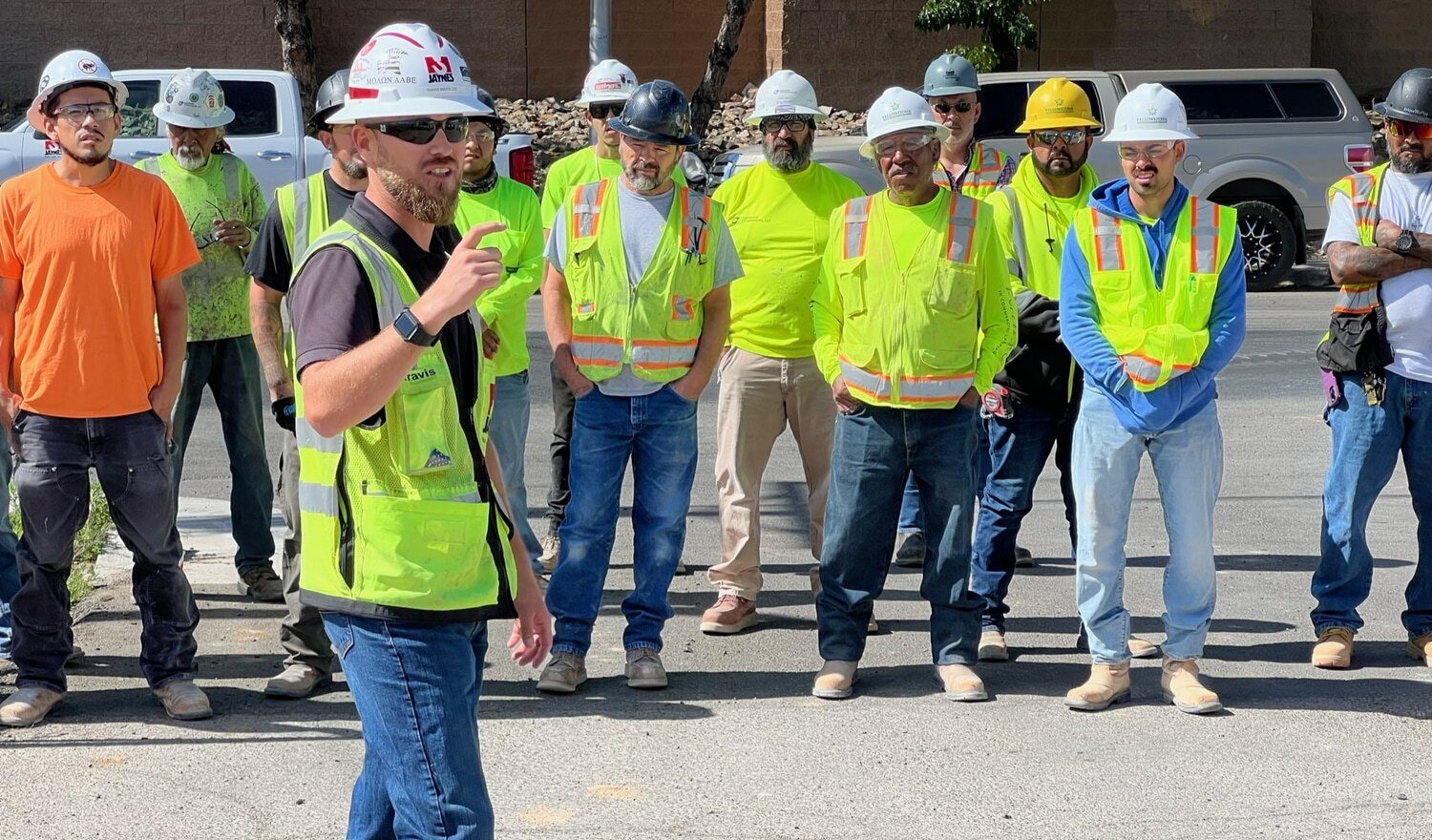
Construction Safety Week Interview with Travis Massegee, Jaynes Corporate Safety Director
May 5th-9th is Construction Safety Week, the construction industry’s annual safety-focused week to promote worker safety and wellness. It’s an opportunity for people, companies, and the entire industry to recommit to doing all it takes to bring everyone home safely.
And it presents a perfect opportunity to check in with Jaynes’ Corporate Safety Director, Travis Massegee, for a Q&A on safety at Jaynes and the trends and innovation he’s seeing in construction safety.
Travis was a dominant force in establishing and improving the safety programs and updating the safety curriculum, earning Jaynes the AGC Construction Safety Excellence Award this year.
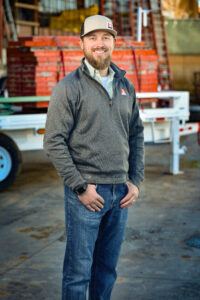
Jaynes Corporate Safety Director Travis Massagee
Travis’ responsibilities at Jaynes include developing safety programs and designing and continually improving company-wide safety policies, procedures, and programs that comply with OSHA, state, and local regulations. Educating project teams on industry best practices to increase employee safety is a professional passion of Travis’.
What’s your approach to getting buy-in on safety awareness?
My job isn’t just about compliance. I stress that safety is intertwined with business objectives and project success. The primary goals are ensuring projects stay on track, protecting Owners’ budgets through reduced incidents and claims, and maintaining Jaynes’ reputation as a trusted, safety-conscious builder. I try to get all of Jaynes to buy into a few simple concepts: safe projects are profitable projects, but even more importantly, that safety is a team effort.
How would you define a strong safety culture in the construction industry?
A strong safety culture is one where safety is embedded in every aspect of the organization, from leadership commitment to jobsite production. It means that safety is not just for compliance or an obligation, but a core value that guides our decision-making.
I instill in the Jaynes safety culture that everyone from our CEO to the newest apprentice understands their responsibility for their safety and the safety of those around them. Research shows that safety scores improve when workers speak up about hazards, stop work without fear of retaliation, and collaborate well to solve safety challenges. A strong safety culture is also proactive. When we plan well to anticipate risks, we increase safety. But there’s no silver bullet. Through planning, training, near-miss reporting, and safety programs like pre-task plans and toolbox talks, we stress a 360-degree view of safety. Leadership sets the tone by visibly supporting and participating in safety initiatives and ensuring that resources and training are always available. I am glad the management team here unconditionally supports and helps improve our safety culture.
How does Jaynes’ management back your efforts as Director of Safety?
Executive management support is the foundation of our safety program. Every new hire is introduced to each Jaynes executive to discuss their background, safety knowledge, and career goals. The importance of safety is a key topic in these introductions.
We also host a monthly Executive EH&S meeting to review safety issues. Project safety scores, Subcontractors’ safety practices, and Jaynes employees needing additional safety coaching are common talking points. Executive team members and our General Superintendent typically travel with me to projects facing safety issues. The management team here is fully engaged in improving our safety culture.
Tell us about how Jaynes strives to reduce risk exposure to employees.
Risk Identification starts before boots hit the ground. My department works with our Estimating Department on projects that have high-risk activities or unusual construction conditions. The goal is to identify and design out or create controls proactively. Each project begins with a Pre-Construction Safety Evaluation. At this meeting, the Project Manager, Superintendent, and Safety Representative review Owner requirements, site logistics, schedule, drawings, Subcontractor scopes, high-risk activities, security needs, emergency response capabilities, and more. This evaluation creates a unique WorkSafe Plan that is reviewed at the Project Turnover and updated at each Subcontractor Pre-construction Turnover. The plan is communicated at every project-specific Safety Orientation during mandatory safety meetings before project launch. In all Foremen’s meetings, in crew-level safety huddles, weekly Supervisors’ meetings, and weekly all-hands safety meetings, we try to make the focus on safety inescapable.
Can you talk about how work is planned safely at Jaynes and how you determine that planning procedures are effective?
Pull planning has been crucial in developing safe work methods at Jaynes. We have integrated our “12 Life-Saving Commitments” into this process. All project teams starting a job organize and facilitate an initial meeting. At this meeting, the Foreman from each trade places a small pictogram of the corresponding lifesaving commitment on tasks taking place that week. Once each Forman has completed the plan, we identify and define high-hazard activities and adjust activities to create a better phase of work to advance a safer work environment. This also determines if the project team needs additional support from the Safety Department during high-hazard activities.
You talk about employee buy-in. How do you encourage worker involvement and participation in your safety programs?
Our executives and my safety team encourage people to be as involved in the safety process as much as possible. Over-communication is fundamental for project leaders at Jaynes. For example, Subcontractors are expected to speak through teaching moments or Q&As during toolbox talks. We have moments like this throughout the construction process where we use meeting time to address safety and ensure constructive input. We have safety incentives for projects with “Safety Shoutouts” or “Good Catch.” These incentive programs reward field managers with bonus points in an annual scorecard. Then, the Safety Department will recognize the highest hazard and most common observations of the month for all our projects. Project team members who contribute the most to increasing project safety by making the most helpful observations are recognized and rewarded by the Safety Department. These programs now formally acknowledge and reward employees who contribute to improving our safety program.
What are the elements of your safety training, and how do you know the training received was effective?
Jaynes has assembled a “Mobile Training Center” to conduct onsite training for all craft workers. The 18’x8’ enclosed trailer is equipped with a 65” monitor with AI language translation software to ensure the message is delivered to everyone. It’s outfitted with Fatal Four training aids and material for fall protection, electrocution hazards, and falling/dropped objects. My department also teaches Jaynes’ “12 Life-Saving Commitments” at the trailer. Creating “Task Specific Training” and delivering them to entire project teams during lunch and learning sessions adds the latest safety best practices to our Subcontractor’s safety culture. The goal is always to increase worker safety. We’ve also created the “Jaynes Safety Academy,” which specializes in educating craft workers on achieving a safe and long career. By the way, it’s common for craft workers to work here at Jaynes for 30, sometimes even 40 years.
Can you tell us about how you manage Subcontractor safety?
Jaynes follows the industry standard of reviewing subcontractor qualifications, safety plans, and standard screening. But we also uniquely approach this. In areas of the Southwest, there is sometimes a small Subcontractor pool. So we have taken on the task of educating each subcontractor on “The Jaynes Way,” which is essentially a culture of promoting excellence. Our Subcontractor mentorship program helps project partners dovetail into our safety plan, and we can pass on our learned safety best practices. Jaynes understands that we are a small piece of a large puzzle, and our mission is to ensure our team’s safety and help create a safer industry.
What drives Jaynes’ safety culture, and how are workers, at all levels, recognized for their contributions?
We’ve implemented a recognition program for our Superintendents and Foremen, in which they get graded on their team’s safety performance. It involves toolbox talks, safety-scored inspections, training, observations, and incident procedures. We also track and measure leadership activities such as lunch and learns, safety shoutouts, and subcontractor safety performance. We conduct multiple “all-hands” events throughout the year to improve our company-wide safety culture. Our “100 Days of Summer” event and “Stand Up for Safety” job site tours are notable. My team also participates in PEER Group activities, so we always have a safety representative at an event. We hold separate events for the family members of Jaynes employees, for example, having the fire department present on fire safety for families and children. Our safety culture doesn’t stop at the project site; our “Safety Brings You Home” program focuses on including team members’ families in safety education on safe driving, fire prevention, and health.
What innovative things is your Safety Department doing?
I think three of our initiatives would be considered innovative. First, our “Industrial Athlete” program starts by scanning willing employees with AI technology that identifies problem areas. This involves certified personal trainers educating employees on the importance of warming up, stretching, and overall health awareness. We also deliver face-to-face physical conditioning coaching from third-party personal trainers at our job sites.
Second, our Jaynes Clinic is a comprehensive on-site healthcare facility staffed full-time by healthcare professionals. The clinic manages all kinds of general family medicine that an employee and their family might need. This includes basic first aid, lab work, physical exams, prescriptions, vaccinations, diagnosis, and treatment of common ailments. It also establishes a “first line of defense” against any work injury that may occur.
And third, we participate in an independent, competitive peer ranking of our safety program as a member of American Contractors Insurance Group (ACIG). ACIG is an industry association of General Contractors who share best practices on safety, saving lives, preventing injuries, and reducing the overall cost of risk. ACIG runs seminars for members on best practices in safety, which have greatly enhanced Jaynes’ safety culture. Subject matter experts from ACIG also measure our safety program and project performance and offer expert analysis on the latest industry innovations to assist Jaynes’ goal of continuous improvement of our program.
For more details on safety at Jaynes, check out the blog on Jaynes’ recent win of the prestigious 2025 Associated General Contractors of America Construction Safety Excellence Award.